Project information
Private dwelling featuring SIP panels
Completion date: 2011
Building type: Private housing
Location: Santo Domingo, Chile
Architect: Alejandro Soffia & Gabriel Rodolpy
Structural Engineer: José Manuel Morales
Timber supplier and erector: Unknown
Timber elements: SIP panels for floors, roof, internal and external walls and stair core. External treatment - Wood Cladding
CASE STUDY:
CASE EN PANEL SIP, CHILE
Design Brief:
The brief from the client was for complete rationalisation, exploration and optimisation of the structural and dimensional qualities of SIP panels. In order to maximise openings and volumes within the dwelling the building needed to be constructed from a series of 'standard' parts.

Design Development:
Two components were designed to act as a 'wall' or ' split level', in 1220 x 2440 x 114mm or 1220 x 4880 x 210mm respectively. To reduce waste onsite, these components needed to be designed into a repeatable pattern that could create dynamic spaces and room sizes for different uses without the need to cut or alter panels. This led to a sequence of spatial model configurations using a basic 'space' formed of 2x 'wall' panels and 2x 'split level' panels, as shown by the diagram opposite and the system as a whole below;

Exploded Axonometric of a 'Space' from
2x 'Wall' & 2x @Split level' Panels
Analysis:
In order to replicate the standard 'space' the sizing of the panels was crucial to forming successful, usable spaces, each of the rooms looks to provide a generous space and the sizing allowed to create two smaller rooms on the ground floor that could be study or bedroom space. One driving factor of a panel width looks to be that it forms a WC, therefore needed to give enough width in that 'space', this would then have been combined with the optimum structural width. The thickness of the panel would have been driven by the thermal performance of the insulation and the structural strength of the OSB. Floor to ceiling height and possibly transport limitations would have been the driving factor of the height of the panels.
The SIP house shows that using this construction methodology doesn't have to be limited to the large scale housing development that is then clad to look like a traditional build. This dwelling shows the rigour and design thought that should be carried through many other projects and typologies
These basic 'spaces' were grouped according to programmatic similarities, principle spaces were grouped to the north to take advantage of the sea views. A central circulation core was formed to provide a vertical connection and any split level panel that became externally exposed was made a prominent feature through wood cladding. These sections then formed part of terrace spaces. Each 'space' was designed to have two open sides, so where an open side became exposed to the outside, it received a different treatment. Dependent on the orientation of the open side, it was either, glazed, the edge protection of a balcony, or clad in a subdued metal cladding. In total 71 'wall' and 40 'split level' panels were used to complete the dwelling.

Spatial model of basic shape to form habitable rooms and linking spaces
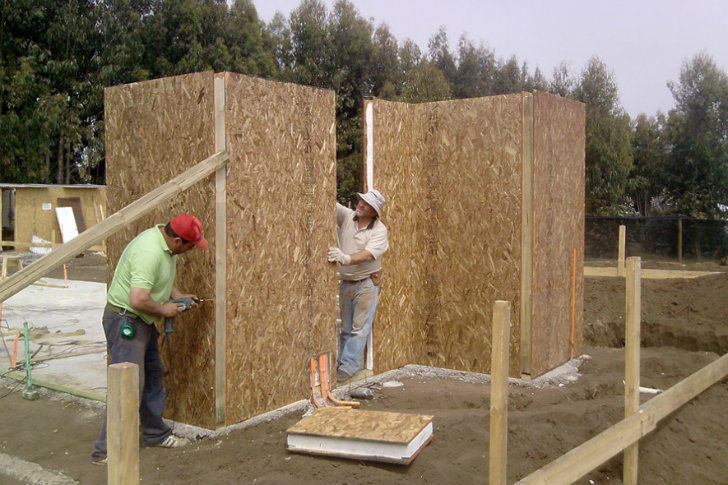
'Wall' Panels being installed

'Split level' Panel completed

Hierarchy of spaces during design to ensure ocean views to principle rooms
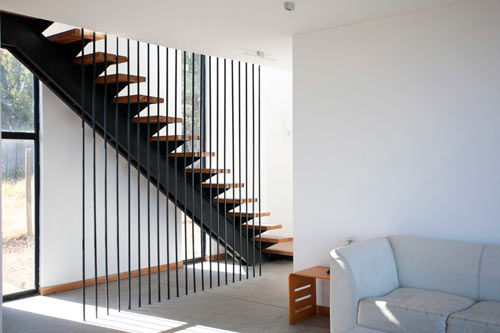
Integration of vertical circulation within dwelling

SIP panels exposed fully clad

external cladding to form usable space and weatherproof structure
Spatial configuration modelling from
step by step diagram

Fig. 1 Completed Construction
Fig. 2 Exploded Axonometric
Fig. 3 Stacking Diagrams
Fig. 4 Project Photos
Application
Although the enclosed precedents demonstrate residential applications, SIPS andCLT panels are used in other instances. They are more commonly found in residential structures because of the maximum spans achievable lend themselves to more appropriate for creating domestic spaces. Schools and other similar structures are able to use these panels as the maximum span available from CLT (15m) still makes their use appropriate. However when attempting to achieve larger spans necessary for offices or industrial units other structural methods become more practical due to often needing to span further.
CLT UK Production It is also worth noting that the production within the UK is currently limited, so many UK precedents have imported their panels from Europe. Unfortunately this adds a premium to the cost, which sheds SIPS panels in a slightly more economical light when compared directly to CLT. It is being explored that the softwood necessary to produce CLT is commonly found in the UK forests, and the probable cause for no UK manufacturing is because there is still little demand for the panels in the country due to the panels being a new innovative construction method.