1.0 Cross Laminated Timber Panels (CLT’s)
This panelling product, is fabricated by binding layers of sawn timber with a contact adhesive, set at 90 degrees to each other, creating an overall solid panel. The panels are all factory produced, the process is quick to repeat on an industrial scale and cheap to produce due to its materiality, which is also taken from sustainable woodland resources.
1.2 Fabrication
Drawings
CAD designs for a structure using CLT’s are produced, either to a manufacturer’s pre-existing design, which typically are entirely made from CLT’s, or to a bespoke design created for a client which might only partially use panels.
Timber Selection
The timber is selected to the specification of the client, including; type, treatment,flexibility and aesthetics. This is repeated for each layer of timber which will compose the final panel. Once selected the timber will travel through a crosscut saw line, which removes any defects ingrained in the material.
Joining Panels
Next the timber is pushed through a structural finger jointer which will fuse the boards into an endless ‘ribbon’. This ‘ribbon’ is then machine cut accurately by a CNC (Computer Numerical Controlled) router device, to the dimensions specified for each panel. The boards are then placed into a high precision planer to produce a smooth, perfectly flat finish. It is essential that this process is completely
accurate, to guarantee the full contact needed by the adhesive between panels, which once pressed will create a full fusion of all elements.
Adhesive Joining
Before this fusion, all boards are laid at 90 degrees to each other (usually the grain is laid vertically on the outer panels, and horizontally for the interior panels), ready for even application of the adhesive, which is usually a polyurethane (PUR) as they are solvent and formaldehyde free.
Pressing
Then the panels move to the pressing process, which involves large high pressured hydraulic machines, to set the pieces together. At the end of the fabrication process the panels are cleaned up, measured and checked, with any defaults or uneven edges being repaired.
Preperation for Site
Penetrations are made in the panels and edges are profiled to match the final construction details. Any connection point to the panel; either for finishes, components or lifting points (for site manoeuvring) are drilled in ready. Lastly the panels are treated with a protective spray sealant, before being packaged for delivery.
CROSS LAMINATED TIMBER PANELS
(CLT)
1.2 Dimension Ranges
Typically the species of wood used for CLT’s depend on the country or region the fabrication process takes place. General species include;
- Radiata Pine
- Douglas Fir
- Spruce
- Larch
1.4 Application & Uses
Typically CLT’s can be used for;
- Flooring
- Walls
- Ceilings
Within a building structure, they can become load bearing and non-load bearing, facilitating the requirement for interior elements and equally can be used for the building envelope. A finished; wall, floor or ceiling layout is achieved by joining individual CLT panels together, either with brackets or traditional joinery techniques
such as; stepped rebate chamfer joins, which can be completed on site or in the factory.
1.5 Advantages
CLT’s offer a wide range of advantages compare to traditional building techniques and materials;
- Waste Reduction
By designing the elements prior to the use on site, there is less waste of general materials. Whereas timber would have been bulk ordered, with spare which would not go into the building, CLT’s allow for precision, with no waste product.
- Lightweight
Timber as a material is also a lot lighter than many others, it is approximately 500 kg/m3, compared to 2,400 kg/m3 of reinforced concrete.
- Strong
Unlike the sawn timber of its individual elements, it can support heavy weights due to its differentiation in compression angles and net density (typically 480-500 kg/m3, with an average mass of 49-52 kg/m2 of a 103 mm thickness panel).
Disproportionate collapse can be avoided by spanning the floor panels in different directions.
Out performs timber studs and joists in fire ratings due to its density.
- Low Cost
Timber in general is considered a cheap material resource, especially when compared to concrete or steel. The pre-fabricated nature of CLT:
-
Reduces costs compared with using traditional building materials
-
Allows for a quicker design programme, therefore reducing the time-cost ratio
-
Results in the need fro less constrction team members required on site.
-
Reducing the material wastage on site.
-
Being lightweight, allows a higher capacity load when transporting to site.
- Rapid Process
The main advantage of this building method is the short completion time units
usually take. Not only is the fabrication in the factory fast, the process on site,
assembling the panels can be done in a fraction of the time of traditional builds.
(Fig ).
- Acoustics
Due to the density and reverberation properties of the thick timber, noise cannot
clearly travel through the material, allowing high acoustic ratings. Other acoustic
systems can be fitted to the panels for added resistance.
- Thermal
Timber has inherent thermal properties in itself, the panelling systems offer an increased thermal property due to increased use of the material. This also helps to avoid cold bridging, a common problem in traditional masonry, or steel constructions.
Benefits from higher density giving better thermal mass and acoustic properties
when compared to other timber frame construction.
- Design Freedom
The pre fabrication element of the product, allows the freedom to test out designs before they are assembled. This could be in a test prior to final fabrication or before delivery to site.
Construction can be digitally practiced and dispatch arranged accordingly to
optimise erection of the structure.
- Sustainability
The timber used for the construction of prefabricated products is sourced from sustainable copse’s and other resources, it has a low embodied energy and is easily recycled at the end of a buildings life cycle into other uses or products.
- Fire resistance
CLT’s are inherently good at resisting fire and heat. This is because the thick
cross-section density, chars at a slow and predictable rate. CLT’s are categorised under heavy timber, which means the product is not reliant on linings or fire resistant treatments. However these can be added to further increase the resistance rating (Fig ).
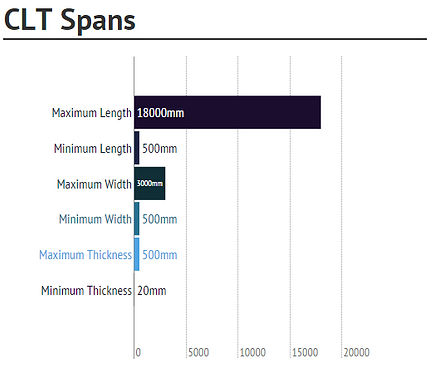
1.6 Disadvantages
- Weathering
Generally softwood is used in the production of CLT’s, it has low natural durability when applied in exposed environments and is not recommended for untreated or unclad use outside. Facade are used to protect the vulnerable material, or repeatedly added chemical weathering treatments.
- Termites
In many European countries such as Australia, termites can be a issue, so keeping the timber panels off the ground would be a required consideration in these climates.
- Early decisions
As much as the ability to have an early, testable design process of a building is an advantage, it is also a disadvantage to the CLT’s. It restricts the changeability of the design through the building process and all decisions, certainly important structural ones, will have to be made and set before the building on site begins.
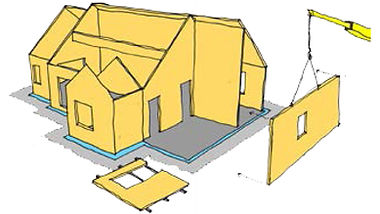
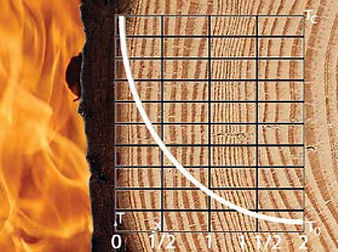
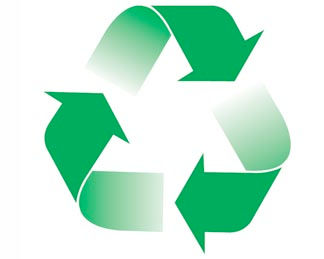

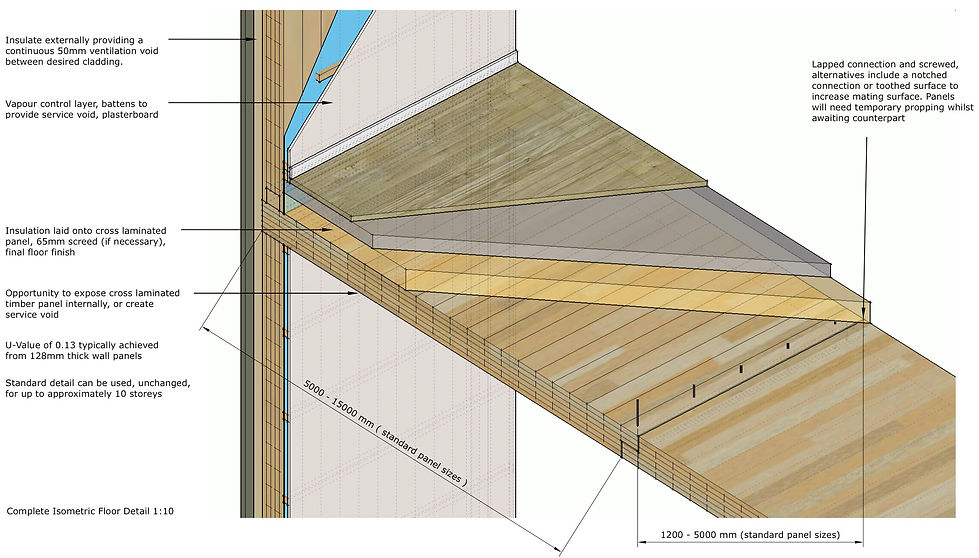

1.3 Design & Construction Considerations
- Transportation may constrict size limitations of panels
- Site access could restrict panel size
- Structural openings need to be decided prior to manufacture



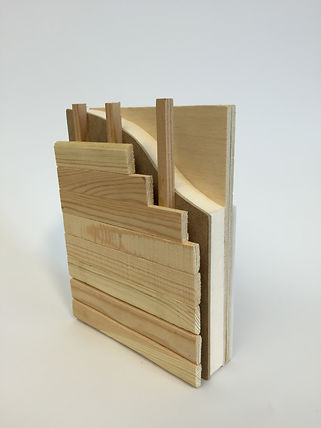

Fig 6. Recycle Logo
Fig 7. Panel Construction Sketch
Fig 8. Fire Resistance
Fig 9. Site Constuction