
Structural Insulated Panels (SIPs) are high performance thermal efficient building panels which are made by ‘sandwiching’ an insulating layer of rigid foam between two skins of timber structural panels. These structural boards or panels could be Oriented Strand Boards (OSB),Fibre Cement, Metal Sheet or Plywood. Core panels or rigid foam are usually composed of Polyurethane Foam (PUS), Expanded Polystyrene (EPS) or Extruded Polystyrene (XPS). If specified during the manufacturing process, a structural adhesive is introduced to bind the foam cores to the skins of the panel during the process of lamination.
Fabrication process
The SIPs fabrication starts with the production of the building design in CAD format, panel manufacturers then convert these drawings into ‘shop drawings’ that can be connected directly into the Computer Numerical Control (CNC) fabrication machines or in some cases, used to measure and cut these panels by hand. Chases are then formed in insulation cores for electrical wiring. After the manufacturing process in the plant, these panels are then shipped to various sites for usage.
Panel Dimension Ranges
Based on standard sizes, SIPs are manufactured in dimensions ranging from 1200x2400mm to large sized 2400x7200mm.
The thickness of the SIPs ranges from 112.5-306.25mm, which provide a range of R-values (the rate of resisting conductive heat flow) that comply with insulation requirements in various climatic zones.

Advantages of SIPs
The advantages of SIPs are categorized under architectural, cost benefit, construction process and environmental benefit; and they are discussed below:
-
High quality construction process
-
Lower long-term maintenance costs for end users
-
Ease of construction with steep learning curve for the craftsmen (installers)
-
Construction life-cycle is drastically reduced
-
Increased builders production capacity
-
Less framing lumber consumed
-
High energy efficiency
-
Less noise pollution produced during construction process
-
Less construction waste, as materials are easily reused
-
Heat loss is drastically reduced as a result of low U-value of the panels
Disadvantages and Limitations
-
Improper sealing of joints during installation could compromise the relative strength of the inner cores, as thus, compromising the structure of the panel on the long run
-
It requires highly special skills to put together properly in construction sites
-
Unfavourable site conditions such as high velocity wind pose as strong issues against the installation of large sized SIPs in construction sites
-
Since electrical ‘chases’ should be pre-routed in panels, rigorous pre-planning is necessary
-
Cannot be used in designing open spaced areas in lower floors of buildings withoutsecondary support system
-
Manufacturer must check against bug and termite attacks on foam core insulation which could seriously impact the structural performance of the panel
-
Lifespan of the panel is directly proportional to the lifespan of the adhesive used.
Application and Uses
Based on the characteristics of SIPs, bonding the foam core to the stiff external panel, produces a web-and-flange structural strength across the length and breadth of the panel, making it act like the
i-section. This adds up to the characteristic compressive strength of the panel.
STRUCTURALLY INSULATED PANELS
(SIPS)
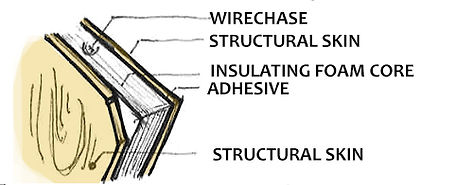


Design and Construction Considerations
-
Foundations; SIPs can be altered on site to fit a non-level or an out-sized foundation
-
Window and door openings should be sized accordingly due to the slight difference in thickness of the SIPs in relation to the stick-framed wall
-
Material Handling and site conditions; Small dimensioned Sips can be handled and installed by hand, but the large sized 2400x7200mm panels require large equipment such as cranes for unloading and installation

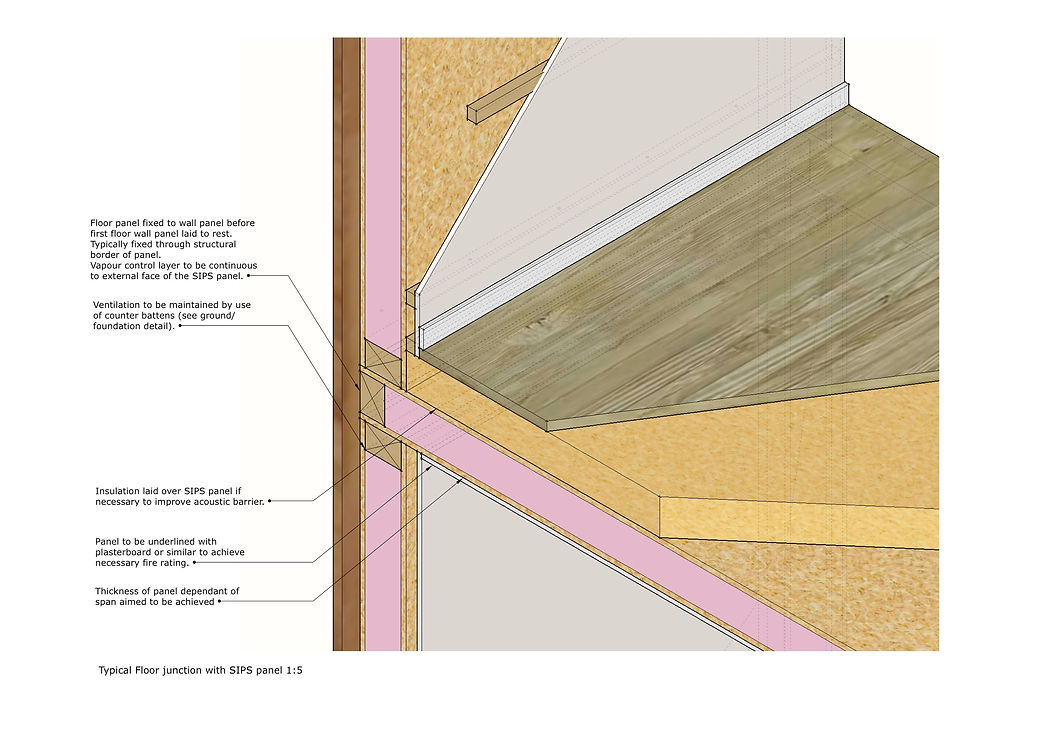

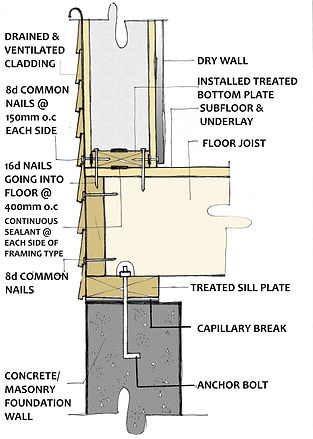
Other uses and applications of SIPs include, but are not limited to;
-
Walls for buildings
-
Roofing of houses
-
Used as timber frames
-
Where insulation for a large span and voluminous interior spaces of timber framed structures are required, SIPs are the most applicable option

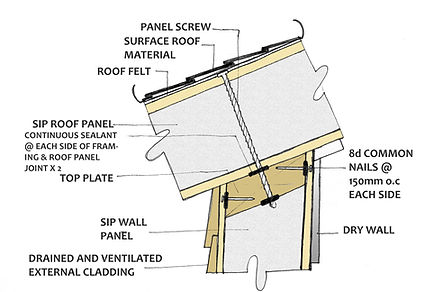
Typical Wall Horizontal connection
Typical Roof -to-wall Connection
How wires run in Chases within a SIP
Structural Analysis
-
Axial strength of the vertically placed panel is increased as a result of proper bonding of foam cores with external hard boards which makes it behave like a slender I-section steel beam
-
Panels have the ability to resist Bi-axial stress as well as lateral shear forces which makes them applicable for use as floor and roof in buildings
Typical Wall to Ground Detail
a. Door and Window openings on SIPs
b. Typical SIPs roof connection to structural kingpost
Typical SIPs Dimension
How SIPs behave like an I-section Steel
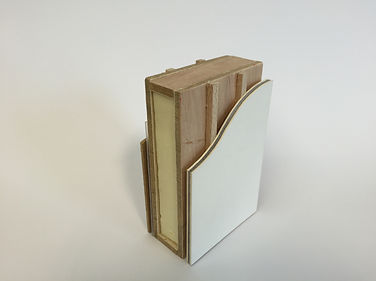